Technical ceramics are a unique material with exceptional properties that allow for applications that were once considered impossible. Be it cutting tools, electrical engineering, or medical technology, they offer numerous benefits across a wide range of applications.
Thanks to the ceramics’ excellent resistance to wear, chemicals, and high temperatures, extreme hardness, and favorable electrical properties, technical ceramics manufacturers can develop high-performance and innovative solutions and products. In today’s blog, we share an overview of the most commonly used technical ceramics in injection molding.
What are the common industrial ceramics?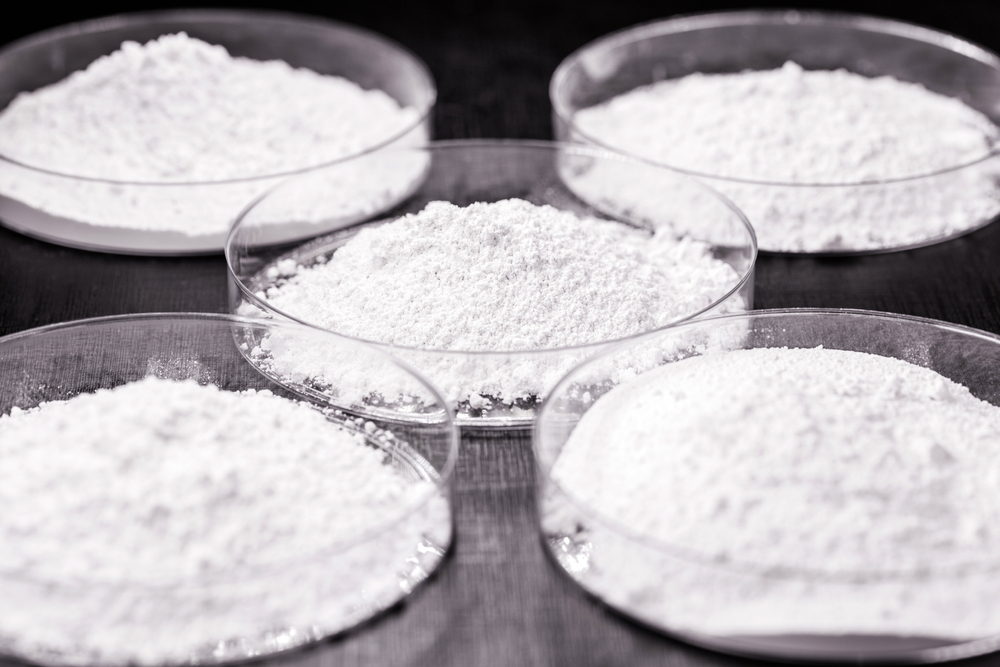
Let’s have a look at some of the most common ceramic materials and their properties and applications:
Aluminum oxide (Al2O3)
Aluminum oxide is one of the most frequently used materials in injection molding. It has various degrees of purity and different properties, which can be adjusted, and it is available in both fine-grained and coarse-grained variants. Main properties of Al2O3 include:
- Moderate to exceptionally high mechanical strength
- Excellent electrical insulation
- High hardness
- High compressive strength
- Good gliding properties
- High wear and corrosion resistance
- Moderate thermal conductivity
- Operating temperature from 1832°F to 2732°F
- Low density
- Food compatibility and bioinertness
Some common applications include catalyst carriers in the chemical industry, heat-sinks, regulator and seal discs for water valves and taps, resistor cores and substrates in the electronics industry, and heavy-duty forming tools.
Aluminum titanate (Al2TiO5)
An exceptional property of Al2TiO5 is its excellent resistance to thermal shock. Although they have low strength, parts made of this material are capable of withstanding sudden changes in temperature, in ranges of up to several hundred degrees, without suffering any damage. Other important features of aluminum titanate are:
- High thermal insulation
- Very low thermal expansion
- Excellent chemical resistance
- maximum operating temperature of 1652°F
- Minimal interaction with molten metals
These properties make it the preferred choice for use in metallurgical melting and foundry technology. In the future, it could play an important role in energy and automotive technology, for applications such as thermal insulation for fuel cell components.
Aluminum nitride (AlN)
This high-performance ceramic features exceptional electrical insulation and thermal conductivity, which make it excellent for use in microelectronics and power electronics. It’s often used as a substrate in semiconductors, and as a heat-sink in high-performance electronics and LED lighting technologies. Aluminum nitrate’s main properties include:
- High capacity for electrical insulation
- High thermal conductivity
- Good metalization capacity
- Low thermal expansion
Zirconium oxide (ZrO2)
Zirconium oxide or zirconia has extremely high crack resistance, unlike other ceramics. It also has very high thermal expansion, which is why it is often used for joining steel and ceramics. Additionally, some ZrO2 types can also conduct oxygen ions. Other important characteristics of zirconia are:
- Low thermal conductivity
- High fracture toughness
Silicon carbide (SiC)
Silicon carbide has properties that are very similar to those of a diamond. Its variants include sintered silicon carbide (SSiC) and silicon infiltrated silicon carbide (SiSiC), the latter of which is especially suitable for the production of large-volume complex components. Their properties include:
- High hardness
- Low density
- Low linear expansion coefficient
- High thermal conductivity
- Maximum operating temperature of 3272°F
- Wear and corrosion resistance at high temperatures
Looking for reliable technical ceramics manufacturers?
Whether you’d like to learn more about the process of sintering, or you’re looking for an experienced partner to carry out your project, Wunder Mold is here to help. Our skilled, knowledgeable, and dedicated team of specialists will work closely with you to understand the specific requirements of your application and provide you with the best possible solution. Get in touch with us by mail at sales@wundermold.com or give us a call and let us know how we can help.